Image may be NSFW.
Clik here to view.
取材・写真・文/大草芳江
2019年06月25日公開
自然の恵みを積極的に生かし、
環境負荷の少ない持続可能なものづくり
蛯名 武雄 Takeo Ebina
(産業技術総合研究所 東北センター 化学プロセス研究部門 首席研究員)
東北で豊富に産する粘土を原料とした高機能な膜材料「クレースト」を開発し、その工業化により東北の産業界に貢献したとして、産業技術総合研究所東北センター化学プロセス研究部門首席研究員の蛯名武雄さんが第68回(平成30年度)河北文化賞を受賞しました。クレーストは厚さ1ナノメートル(10億分の1メートル)の板状の粘土結晶を緻密に積層したフレキシブルな膜材料で、既存材料にはない高いガスバリア性と耐熱性を有する膜材料として、幅広い産業分野で製品化が進められています。クレーストの生みの親である蛯名さんに、開発の経緯や研究にかける想いなどを聞きました。
※ 本インタビューをもとに「産総研東北ニュースレターNo.48」を作成させていただきました。詳細は、産総研東北センターHPをご覧ください。
1.高機能な粘土膜「クレースト」の開発と、その工業化による東北への貢献
―このたびは河北文化賞のご受賞おめでとうございます。今回の受賞対象となった粘土膜材料「クレースト」はどのようにして開発されたのですか?
◆ 東北で豊富に産する粘土をバリア材に
Clik here to view.
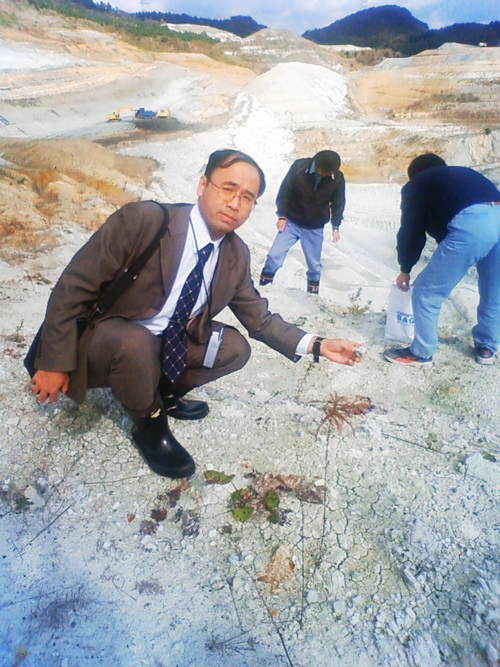
【写真】ベントナイト鉱山(宮城県川崎市)でサンプルを採集する蛯名さん
私が東北工業技術試験所(※)に1993年入所した当時から、すでに研究室のテーマとして取り組んでいた、東北地方で豊富に産する「ベントナイト」と呼ばれる粘土を研究してきました。
※ 産総研東北センターは、1928年、国立工芸指導所に始まり、東北工業技術試験所となり、次に東北工業技術研究所へ改称し、2001年に産総研東北センターとして組織再編された。
一般的に粘土と言えば、焼き物の原料というイメージが強いと思いますが、ベントナイトは、焼き物には適していません。ベントナイトの特徴として、例えば、水をドロドロにする性質(保水性)や、水を通しにくい性質(遮水性)があります。そのような性質を活かし、当初は廃棄物の処分場から有害物質が漏れ出すことを防ぐための浸水バリア材として、ベントナイトの研究をしていました。
◆ 粘土を薄くするほどバリア性が向上
最初はベントナイトを圧密した塊をサンプルとして、水のバリア性を測定していました。ところが、いつまで経ってもなかなか水が染み出してこないので、サンプルを薄くすることにしたのです。すると、ベントナイトの層を薄くすればするほど、水が通るスピードは遅くなり、膜状にまで薄くしたものが最もバリア性が高い、という意外な結果が出ました。その理由は、慎重にサンプルをつくるために、厚さ1ナノメートルの板状の粘土結晶が一方向に整然と並びやすくなり、それらが多層的に重なり合うことで、通り抜ける水分子にとって"邪魔板"の役割を果たすためだということがわかりました。
Image may be NSFW.
Clik here to view.
【図】粘土膜の構造と、バリア性の発現メカニズム
◆ 粘土を用いた膜の研究を開始
Clik here to view.
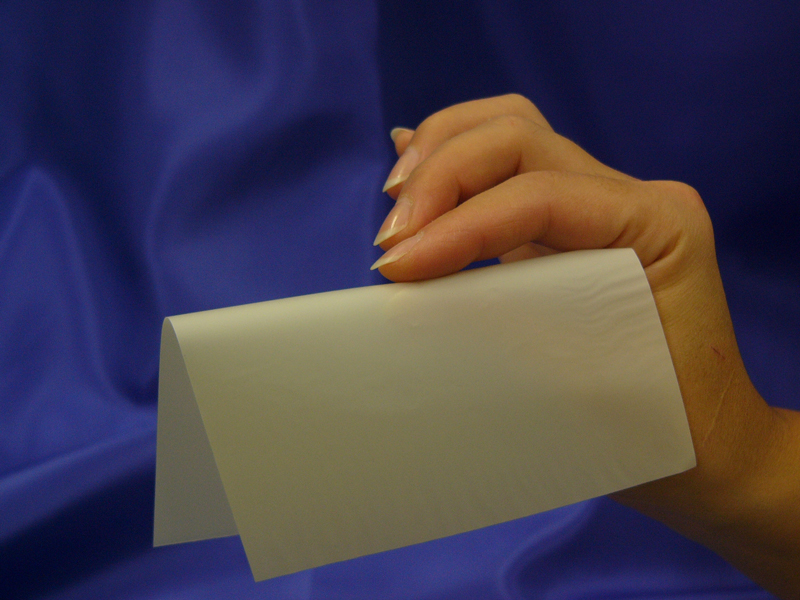
【写真】高い耐熱性と驚異的なガスバリア性を有する粘土膜「クレースト」
工業用途として、気体を透過させない「ガスバリア」のニーズが非常に多くありますが、プラスチックに粘土を混ぜることでガスバリア性が高くなることが知られていました。さらに、高温で溶けたり燃えたりするプラスチックとは異なり、粘土は耐熱性が高い特性もあります。そこで、プラスチックが使えないような高温下でも使える耐熱バリア材料として、粘土膜を実用化するアイディアが浮かび、2003年、当時の上司だった水上富士夫氏から、高圧水素ガスシール材の検討を指示されました。そして、この粘土膜の性能をテストした結果、高い耐熱性とガスバリア性があることがわかったのです。完成した粘土膜は「CLAY(粘土)」と産総研の英文略称である「AIST」から「クレースト(CLAIST)」と名付けられました。
―開発した粘土膜材料を、どのようにして実用化にまで結びつけていったのでしょうか?
◆ バリア機能を工業用途に積極展開
2004年以降、耐熱バリア材料としての粘土膜を産総研のシーズとして、プレスリリースや展示会等で積極的に発表し、「この新しい材料をどんな用途に使えますか?」と、幅広く問いかけました。2010年までに国内外から約400件もの技術相談を受け、これらの情報も基礎として強い特許群の構築を行いました。
Image may be NSFW.
Clik here to view.
【写真】粘土膜のサンプル帳。ゼオライト粘土膜やカキ殻配合粘土膜など、様々な実施例を作成し、特許群の構築を行った。
◆ 第一号の製品化はアスベストの代替材料
Clik here to view.
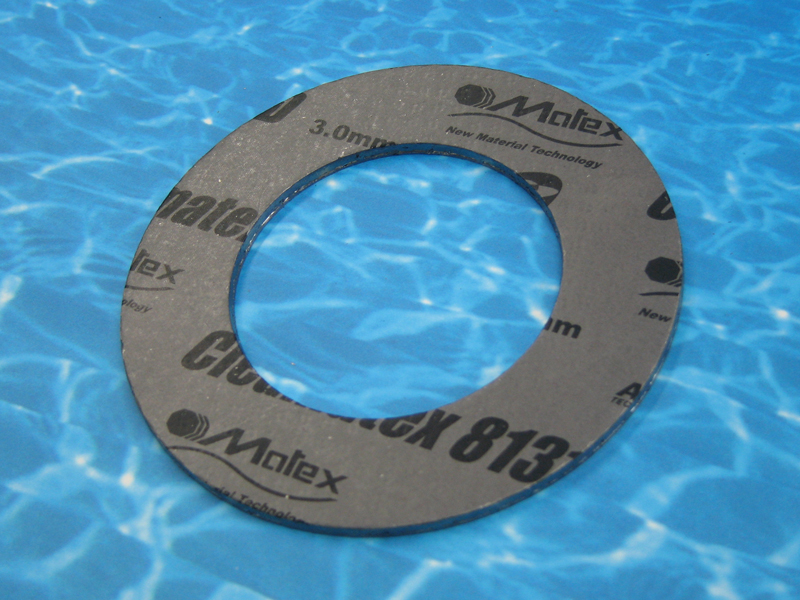
【写真】クレーストをコートし、アスベストを使用しないガスケット(ジャパンマテックス)
クレーストの第一号の製品化の取り組みは、アスベスト(石綿)を使わないガスケットの開発でした。ガスケットという、工業用配管間のつなぎ目の隙間を埋めるガス漏れ防止用のシール材として、それまでアスベストが使われていましたが、健康への影響があるとして、代替材料の開発が急がれていました。そこで、ジャパンマテックス株式会社(大阪府)とアスベスト代替ガスケットの共同開発を始めました。2007年には製品化に成功し、発電所や化学プラントなどに広く導入されています。
―クレーストの工業化により、東北にはどのような貢献があったのですか?
◆ 東北ゆかりの原料と技術、企業でつくる
Clik here to view.
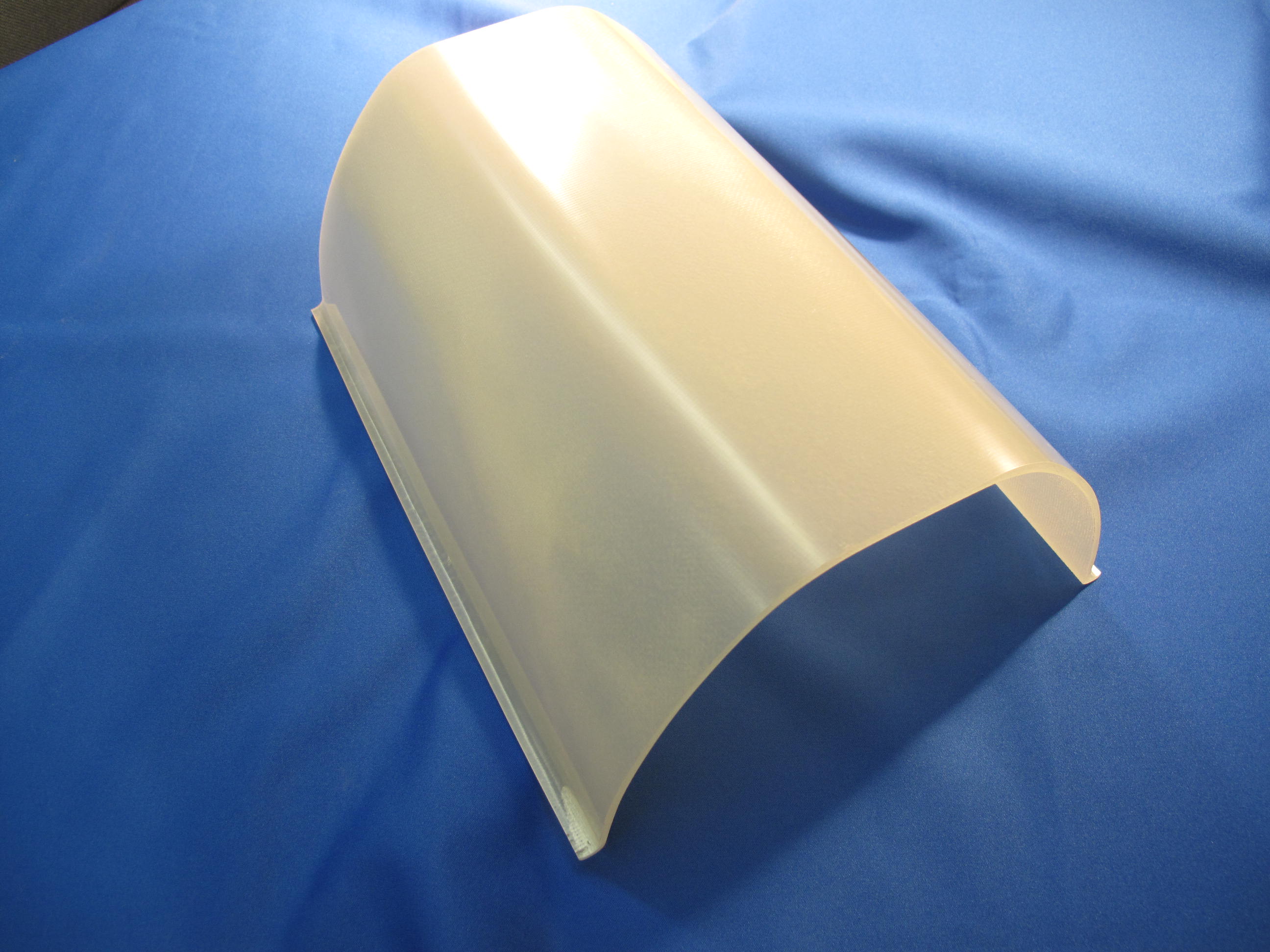
【写真】燃えない照明カバー(宮城化成)
原料となる粘土も、技術も東北発ですので、東北で生まれたシーズを東北地方の企業に使っていただくことで、地域活性化に貢献したいという想いがありました。そこで、株式会社宮城化成(宮城県)とは、燃えないプラスチック材の共同開発を行いました。製品化までには6、7年を要しましたが、新幹線の天井材に使えるような、燃えない、かつ割れない、安全性の高い照明カバーの開発に成功しました。
Clik here to view.
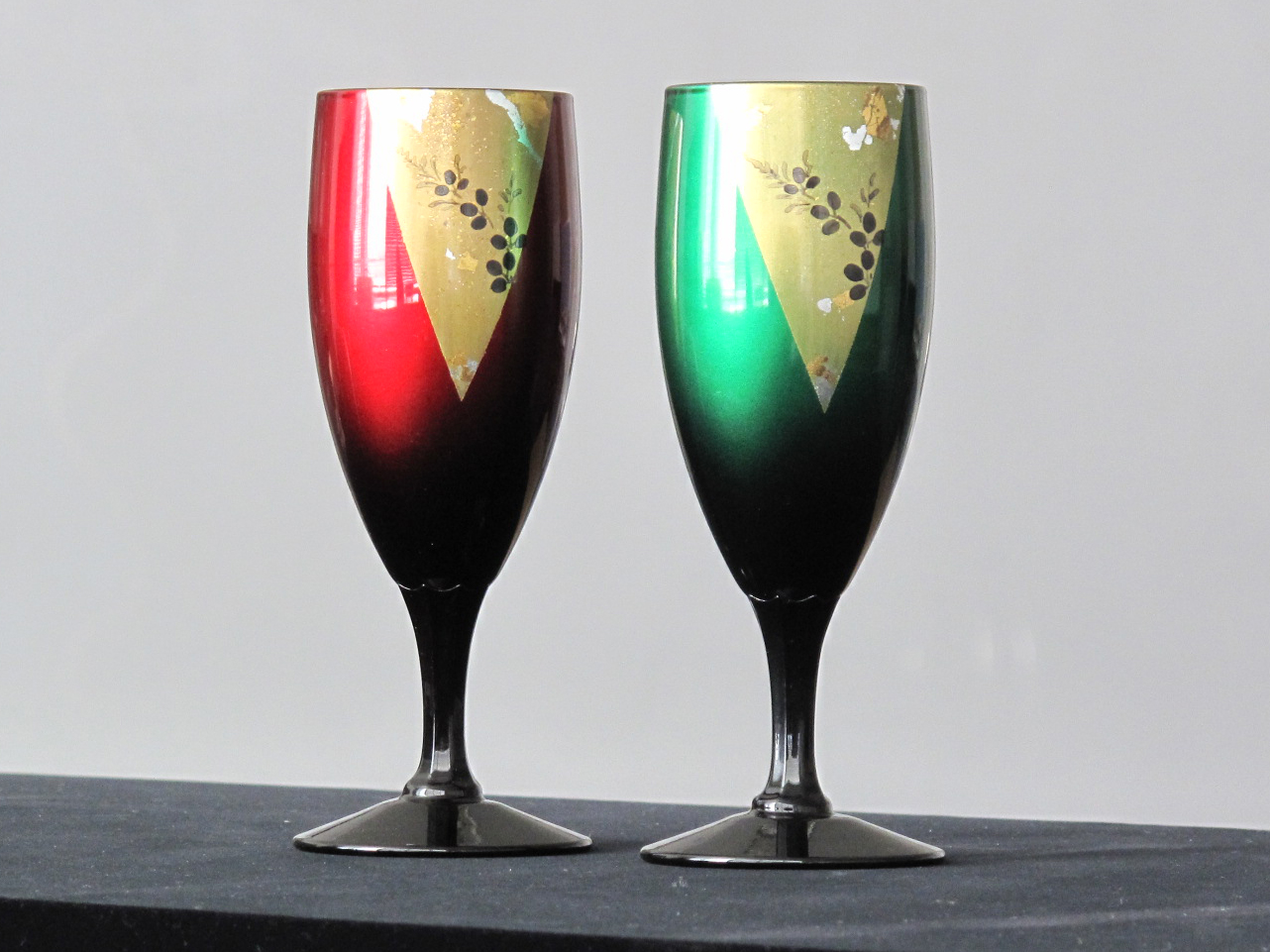
【写真】食器洗浄機対応玉虫塗で、見る工芸から使う工芸へ(東北工芸製作所)
さらに有限会社東北工芸製作所(宮城県)とは、食器洗浄機で洗える工芸品の共同開発を行わせていただきました。宮城県指定の伝統的工芸品「玉虫塗」の保護膜として、粘土とプラスチックをナノレベルで混合したナノコンポジットコーティングを開発し、食器洗浄機対応の玉虫塗の製品化に成功しました。これも製品化までには約6年を要しましたが、今でも引き合いが多い製品に育てることができました。
製品を開発する時、資源が東北にあり、研究が東北で行われ、その技術を使った製品化に東北の企業も成功している事例はなかなかつくりづらいと思うのです。しかし今回、色々な方にお会いできた幸運もあって、東北ゆかりの原料と技術、企業で製品を一貫してつくることができました。そのような点を河北文化賞ではご評価いただけたのではないかと考えています。
2.「技術の橋渡し」までの長い道のり
―新たな技術を生み出すことも簡単ではないですし、さらに開発した技術が事業化まで到達する成功事例は、非常に少ないと言われています。それを「東北ゆかりで一貫して実現すること」はなおさら難しいことだと思いますが、研究開発から事業化まで、どのような壁を乗り越えてきたのでしょうか?
◆ 「技術の橋渡し」には時間が必要
産総研のメインのミッションとして「技術の橋渡し」があります。開発した技術を製品化するまでの段階で、周辺技術等が同時に成長しなければ製品化には至らないため、一見すると何も行われていないかの如く見えます。それがいわゆる「死の谷」と呼ばれるものです。産総研としては、この「死の谷」を乗り越え、どのようにして実用化まで結びつく研究開発ができるかを、方法論として体系化しようとする試みを、研究所を挙げて取り組んでいます。私としても、その開発期間をなるべく短くするよう工夫してきたことは事実です。それでも振り返れば、やはり開発した技術の製品化にはそれぞれ6、7年を要しています。
◆ 粘土膜の耐水化が一番の壁
材料開発には20年かかるとも言われています。実際、粘土膜自体は私が初めて開発したわけでなく、1937年、マサチューセッツ工科大学の研究者が「AlSiフィルム」というアルミニウムとシリカでできた材料を提案しており、米国の著名なニュース雑誌にも「永遠不滅のシート材として使える」と紹介されていました。その材料は、私がつくった粘土膜と大体同じもので、用途としては電気絶縁用のフィルムとして検討されたようですが、製品化まで至ったという話は聞いていません。
―1937年に提案された粘土膜は、なぜ製品化まで至らなかったのでしょうか?
その当時はガスバリアフィルムのニーズがなかったことに加えて、耐水化の点で問題があったと思われます。耐水化問題は、私の研究開発でも最後に残った、最も大きな壁でした。
クレーストは、原料となる粘土の粉を水に加えて、塗料のような均一なペーストにして、これを平らな基板の上に塗り、乾燥させて剥がすと膜ができるという、簡単な方法でつくることができます。ここまではよいのですが、問題はここからです。そもそも水に溶ける性質だから粘土が膜になるわけですが、膜になった後、また水に溶けてもらっては困るのです。乾いたガスの遮蔽性(ドライガスバリア性)は非常に高いにもかかわらず、水蒸気バリア性が低いために、粘土膜を工業材として使えないという、決定的な問題がありました。
Image may be NSFW.
Clik here to view.
【写真】クレーストの原料となるベントナイト等を水に溶かしたペーストを手に説明する蛯名さん
焼き物の場合なら、非常に高い温度で加熱することで、無機結晶でも水に溶けない性質に変わるので、耐水性の問題はないのです。ところが粘土をフィルムとして使う場合、あまり高い温度で焼くとパリパリになって使えなくなってしまうため、柔らかいままで使おうとすると、あまり高い温度をかけられないという問題がありました。そのような理由から、粘土膜を開発した後も、どのようにして耐水化させるかが、実のところ最も時間がかかった仕事で、5、6年の歳月を要したのです。
◆ 耐熱性・ガスバリア性・耐水性の3つが揃う、オリジナル粘土膜を開発
―そもそも粘土が水に溶ける性質を利用して膜をつくるのに、水に溶けない性質に変える必要があるという、矛盾する問題を、どのように解決したのですか?
耐水化させた粘土が世の中にひとつもなかったかと言えば、当時もありました。もともと粘土は無機化合物ですが、表面に界面活性剤という有機物をくっつける、「有機化粘土」という方法です。界面活性剤を用いて、本来親水性である粘土の表面を疎水性に変えることで、有機溶剤に混ざるようになり、水には溶けなくなるという前処理が、粘土を耐水化させる、それまでの一般的な方法でした。
ところが、粘土を有機化すると、また別の重大な問題が発生するのです。もともと粘土の特長は、プラスチックが使えない高温で使える点だったにも関わらず、界面活性剤が入ると、高い温度では使えなくなってしまうのです。さらに、粘土膜の非常に高いガスバリア性は、板状の粘土結晶が一方向に隙間なく積層することで発現するメカニズムなのに、そこに有機物がくっつくと、粘土結晶同士がくっつかずに離れてしまうため、肝心のガスバリア性が上がらないことがわかってきたのです。
要するに、どの方法も一長一短でした。そのまま無機物としての粘土は、高い温度で使え、ガスバリア性も高いが、水には溶けてしまう。一方、有機化した粘土は、水には溶けないが、高い温度で使えないし、ガスバリア性も高くない。つまり、耐熱性とガスバリア性と耐水性の3つが揃う粘土膜を開発するのに、非常に苦労したわけです。
苦労の末に開発した粘土は、見た目はこれまでと同じように見えますが、これまでと同様に水系で粘土を膜にした後、ある一定の熱(約100~200℃)を加えることで耐水化する、「加熱耐水化粘土」と呼ばれる粘土です。有機化合物を使わないため、高温でも使え、ガスバリア性も高く、水にも溶けません。2009年に成功したこの開発が実は我々のオリジナル技術で、粘土バリアの用途を広げた一因となっています。先述の宮城化成と共同開発した「燃えない照明カバー」にも、この加熱耐水化粘土が使われています。
Image may be NSFW.
Clik here to view.
【図】従来粘土と加熱耐水化粘土の比較
◆ やるからには売れるまで面倒を見たい
さらに、新しく開発した技術を製品化する段階でも、新規の問題がいろいろ発生します。例えば、「こんな形状に成型しないといけない」といったプロセスの問題であったり「つくった後に掃除をしても剥がれない膜にする必要がある」といった問題であったり。あるいは、製品化で必ず問題になるのがコストの問題ですね。
玉虫塗の事例についても、お客様に見てもらうための美しさを追求する商品ですので、我々研究者の「これくらい綺麗ならよいのでは」という甘い考えが全く通用しませんでした。見た目が白いとかでは使えないので、保護性能を維持しつつ、美しさを持ち合わせることも完全にクリアできるよう、時間をかけて開発をさせていただきました。
そのようないろいろな問題が製品化の段階でも必ず発生しますので、意外と一筋縄ではいかないのです。それでまた原料に戻ってきたり、行ったり来たりがたくさんありますので、自然と時間もかかります。製品化研究をやるからには、論文を書いて終わりでなく、やはり売れるまで面倒を見たい気持ちが強いので、企業と連携させていただく段階もしっかり時間をかけて取り組ませていただきました。その結果が、6年、7年という歳月なのです。
◆ 歴史とは生かすもの
話は少し戻りますが、産総研東北センターが、漆器、木工、工業デザインなどを取り扱う国の機関である工芸指導所をその起源にしていること、また、工芸指導所の発明を基に、東北工芸製作所は「玉虫塗」を製作していることを、東北工業大学の庄子晃子先生が開設した「仙台デザイン史博物館」というWebサイトで勉強させていただきました。
工芸指導所発の、今の言葉で言うベンチャーは、工芸と最先端材料の融合という野心的な取り組みを行っており、戦前ながら、むしろ今の私たちの発想よりも自由で開拓意識旺盛だと感じました。そこで「歴史とは学ぶものでなく今この時に生かすものだ」と思った私は、東北工芸製作所のショールームにアポなしで訪問し、同社の佐浦みどり氏に「何か一緒にできませんか?」と提案して、先述の食器洗浄機対応漆器の開発を始めたのです。
デザイン研究発祥の工芸指導所を起源とする産総研東北センターとして、デザインまで踏み込んでアピールしたいと考えています。新規材料ですから初めからは安くはつくれませんが、高い付加価値をユーザーが認めてくれるデザインの力は強いという認識を持っていますので、ものづくりにデザインを掛け合わせ、高付加価値化の実現を目指しています。
3.「死の谷」を乗り越える原動力
―それほど膨大な壁を乗り越えてきた蛯名さんの原動力とは何でしょうか?
◆ 一緒に走っているからこそ、諦める意識はない
私が頑張れたのは、共同研究する会社側にも頑張る人がいるからです。熱意を持って自社製品の開発に取り組む方々とお話したり、あるいは、ご期待をいただいたりすると、我々の仕事は「技術の橋渡し」ですから、しっかりそのバトンを渡さなければいけないと感じます。一人で走るというより、一緒に走っている意識が強いので、それが心の支えとなって続けることができるのだと思います。
最初にクレーストの製品化に取り組んだ、ジャパンマテックスの塚本勝朗社長(当時)が非常に熱い方で、塚本社長の「今すぐやる・できるまでやる・必ずやる」という行動指針に影響を受けました。いわゆる精神論ですが、塚本社長が「できる」と言うと、本当に製品化していたので、塚本社長の曲がらない信念にひっぱられて、私たちも全くくじけることなく、進めさせていただきました。今でもそうです。
逆に言えば、自分の中で「必ずできる」と信じて取り組まなければ、やってはいられないのですよ。問い合わせの数から割り算すると、約99 %は製品化しないのですから。さらに共同研究などの正式な研究開発をスタートしてから製品化する可能性でも約5分の1です。すると打率で言えば約2割で、打てない打者と同じですよ。とはいえども初めからくじけることは全く頭の中にはありません。一つひとつ成功事例を積み重ねるしかないからです。
◆ めげない理由は、粘土そのものにもある
もうひとつ、私だけの"めげない理由"があります。その答えは粘土そのものにあります。ベントナイトは「千の用途を持つ材料」と言われています。工業利用で千種類あるかと言えば流石に嘘ですが、ポテンシャルという意味では正しく、いろいろなものに使える可能性があります。
なぜかと言うと、まず地球上にたくさんあります。そして、一つひとつ合成する必要もありません。さらに、ベントナイトは食べることもできるくらい、人間に対して安全です。コストだって、もちろん手間をかければ上がりますが、掘って採れるという意味では、目が飛び出るほどの高値ではありません。ほかにも先述のとおり水と混ぜることができたり、有機化すれば有機溶媒に混ぜられたりといった特性もあるので、いろいろな可能性を持つことは事実です。
そんな機能性材料って、大体考えつかないでしょう?普通は新しい材料をつくると「何に使えるの?」という疑問が生じるわけですが、ベントナイトは「千の用途がある材料」と初めから言われているので、「必ず何かに使えるはずだ、ならば使える用途を見つければいいじゃないか」と考えられます。無理な話ではないだろうと諦めずに開発ができるわけです。
実は、研究者の世界には、研究者が注目している流行りの研究テーマというものがあり、研究者は製品にならないと本当はわかっていても、論文を書く時には、枕詞に「これは~の材料として注目されている」と書くわけです。それはなぜかと言うと研究のプロだからです。一方で、研究する前から「これは本気で開発すれば、本当に何種類か用途が出てくるぞ」ということがわかる材料というものがあり、そもそも私は後者の方をやりたいのです。
4.研究の原点は「人類を滅亡から救う仕事がしたい」
―研究者の世界で評価される研究より、産業界で製品化に結びつく材料の研究開発を、蛯名さんが望むようになった原点とは何でしょうか?
◆ 18歳の頃、「人類を滅亡から救う」と決める
Clik here to view.
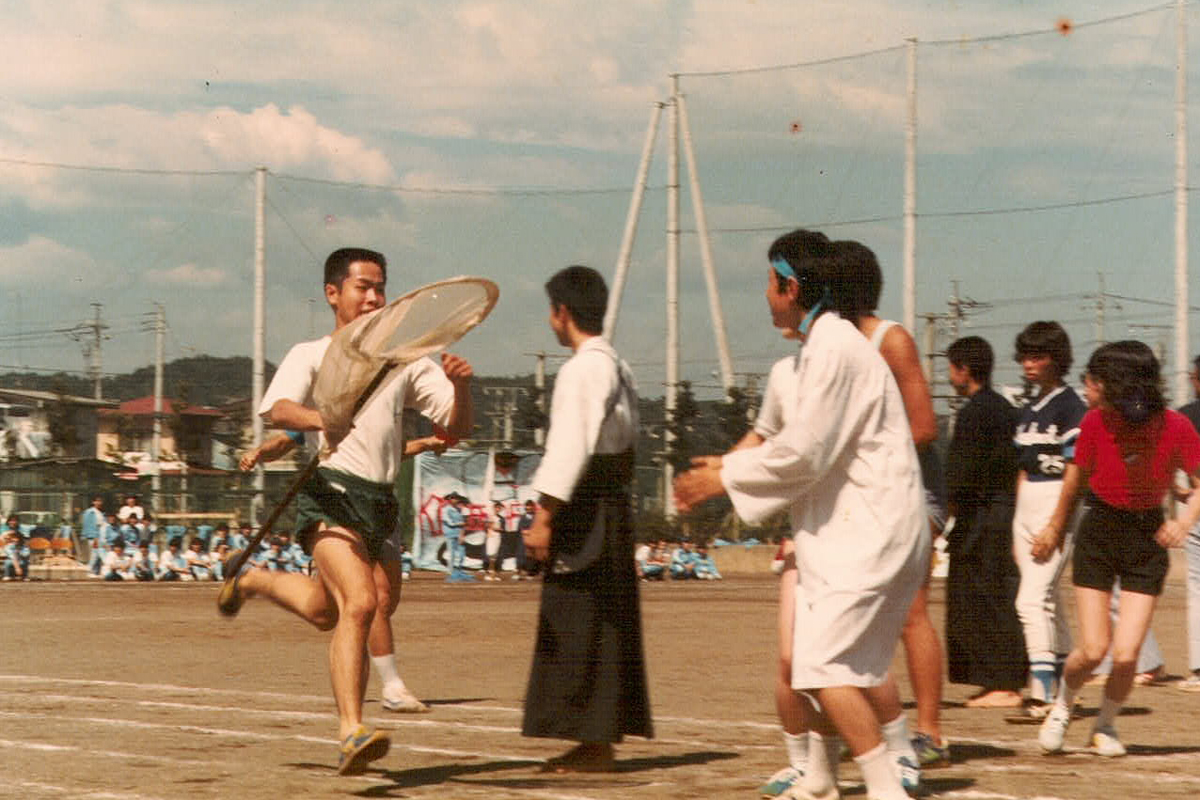
【写真】部活動対抗リレーにて、虫取り網を持って走る高校2年生の蛯名少年。「部活動関係の写真はこれくらいしか持っていません」。
話は高校生の頃に遡ります。1979年、神奈川県立橋本高校の生物科学研究部に、顧問の田口正男先生から勧誘されて入部しました。谷戸(谷間)水田におけるトンボの個体群生態学研究を、フィールドワークでキャッチ&リリースの手法を使って研究し、学会で発表して、一連の研究の仕方をここで学びました。
その頃は、国際的な研究・提言機関「ローマ・クラブ」が「成長の限界」という報告書を1972年に発表してから7年が経った頃でした。それまでは人間の活動が地球環境に与える影響はそれほど大きくないと考えられていましたが、地球レベルで生態系に大きな影響を与えることや資源の枯渇につながることを、皆が考え始めた時期でした。その頃に高校生だった私は、自分の将来について考え、「人類を滅亡から救う仕事をしたい」と決めました。
Clik here to view.
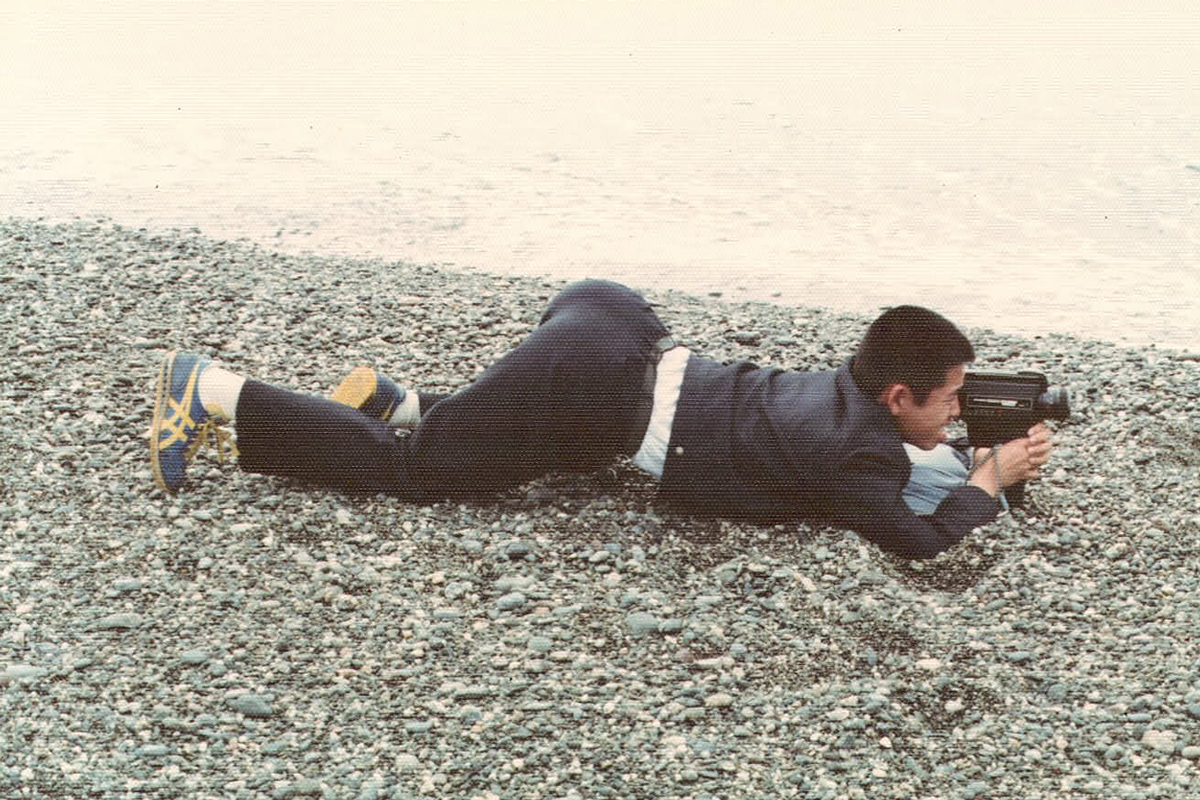
【写真】映画撮影中の蛯名少年。「人類を滅亡から救うことに目覚めた頃の写真です」。
18歳の頃、「人類と環境 ―地球システムの平衡―」という8ミリ映画を制作しました。当時、「夢の島」と呼ばれていた埋立地(現在の新木場付近)へロケに行き、リサイクルの考え方を映像化しようと制作したもので、基本は「人類を滅亡から救う」ことがテーマです。そのためには世の中の役に立たないと困るわけで、「研究のための研究」となると、自分がやろうとしていることの整合性が合わないわけです。
5.自然の恵みを積極的に生かす「めぐみものづくり」
◆ 2010年、「めぐみものづくり」を提唱
地球の平均組成を計算すると、私が開発している材料とほとんど同じです。したがって、採る時も地面から採ってくればよいだけ、捨てる時も地面に捨てるだけでよく、環境負荷がないわけです。サスティナブル社会の実現を志向し、そのような天然無機素材の組成・機能・形状を生かしたものづくりを「めぐみものづくり」として2010年に提唱しました。
例えば、漬物石は、ある特定の条件を満たさなければ、漬物石にはなりません。まず形は、重ねられるよう、下面はある程度平坦で、手で持つ場所はスベスベである必要があり、かつ、重さはある程度付加しつつも、腰を傷めない程度に重過ぎてもいけません。漬物石は河原で拾って来て、不要になれば捨てることができます。もし漬物石を人為的につくるとなれば、面倒ですが、それは河川の力で自然にできるものです。
粘土も同様に、はじめは大きかった石が風化し、雨の力で転がるうちに細かい砂となって堆積し、それが地層深くまで沈み込み、熱の作用と水の追加によって反応釜のようになり、原料が粘土というナノ粒子に変わります。人間は何もせずとも、粘土という安全なナノ粒子が自然につくられるために、私たちが膜をつくる時も綺麗な膜になります。そのような自然の恵みを積極的に生かし、環境負荷の少ない持続可能なものづくりが、「めぐみものづくり」なのです。
◆ 卒業研究での環境浄化の経験が基礎に
「めぐみものづくり」の考え方は、岩手大学の卒業研究時に行った、松尾鉱山の酸性水と北上川の清流化対策の経験が基礎になっていると思います。岩手大学の後藤達夫先生が、松尾鉱山から流れ出る酸性水の中和処理を行い、北上川の清流化に成功し、私もその水分析に携わりました。普通に考えると、自分が外の世界を制御できないように思えますが、中和処理施設をつくり環境浄化ができた経験を経たからこそ、「めぐみものづくり」という考え方を、言葉としてつくることができたのだと思います。
―今後も「めぐみものづくり」をテーマに、研究開発と製品化を進めていくのですね。
◆ 海の流れの多層性に研究を重ねて
はい。私は研究の多層性を、海の流れの多層性に重ねて考えています。私たちの仕事は、基本的には、表面の波を見ているようなものです。サーフィンをしている人がサーフボードから落ちないよう、波の形の時系列的な変化を見て、所作を決め、波に飲み込まれないための日々の問題解決が、私たちの研究開発の8割方を占めています。それに対して潮汐は、4年から10年の国家プロジェクトに当たると考えます。さらに親潮や黒潮といった流れは、もっとゆっくりした流れですが、方向が決まっているという意味で、私の場合、クレーストやバイオマスといったライフワークだと考えています。実は、それよりさらに深い深層海流という、地球を1周するのに千年もかかる流れがあるそうで、私が死んでもつなぐ必要があるもの、それが「めぐみものづくり」です。一番根底に「めぐみものづくり」が流れているので、それぞれの向きが同じ方向とは限りませんが、矛盾していることをやっているとは私自身思っておらず、すべて同じ流れの中で解決できる話だと考えています。
◆ 研究は人を集め、遠くを照らす灯台
この流れの多層性の上下関係を考える時、私は灯台のイメージを持ちます。「灯台下暗し」という言葉があるように、灯台の下は暗いですが、灯台は遠くを照らすものです。人を集め、遠くを照らす研究でなければ駄目ですから、垂直方向で言えば、表層ではなく深層を、研究は指さなければなりません。
つまり、何を言いたいかと言うと、今取り組んでいる日々の仕事は表層でも、研究者は遠くに光を指すことはできます。その先とは「めぐみものづくり」です。それぞれの層は直接つながっていなくとも、遠くを見て研究開発をしようと提言すれば、だんだん皆がそちらを向いていく、その役割は果たすということです。そのように自分の中では理解して、普段は問題解決の仕事を中心にさせていただこうと意識しながら研究を行っています。
◆ 東日本大震災の経験から思うこと
2011年に発生した東日本大震災で、弊所は復旧に関わる半年程度の遅延を経て研究開発を再開しました。震災を経験して思うことは「自然は与えるもの、自然は奪うものであると同時に、やはり自然は与えるものだからこそ人が戻ってくる」ということです。その営みは止むことはなく、また完全には解決ができないものですが、その中で自然に産するものを私たちはどのように活かしていくかが重要だと思います。
2016年からは、森林総合研究所と木質材料の実用化の共同研究も開始しました。海側のみならず山側にも災害はある中、限りある森林資源を守り、どのように利用していくかが、やはり重要だからです。東北センターにいるために、そのような経験もさせていただきました。引き続き、自然と対峙する東北地域において研究開発を続けることができれば幸いです。
◆「Clayteam」設立10周年を迎えて
2003年に開発した粘土膜は、一定のレベルに達し、実用化に至ったものもありますが、汎用材としては技術的・経済的な課題が残されていました。この状況を打破すべく2008年に「クレースト連絡会」を設立し、会員数も飛躍的に増えたことから、2010年に「Clayteam」という産総研のコンソーシアムを設立しました。民間企業と連携し、原料粘土や粘土膜関連技術の提供、連携コーディネート、共同研究、製品評価などの支援を行い、研究開発の大幅な加速につなげています。そして2019年度に、「Clayteam」は設立10周年を迎えます。この間、粘土などのナノ材料を用いた多くの製品開発に成功してきました。ナノに基づく機能を付加価値としたナノテクビジネスは、今後本格的成長を迎えると予想されています。
最後に、産総研関係者とは多くの方々と出会い大変お世話になりました。しかし、現役の産総研の方々については、毎日会うため恥ずかしいですし(笑)、また別の機会もあると思いますので、ここでは触れないでおきたいと思います。
Image may be NSFW.
Clik here to view.
―蛯名さん、ありがとうございました。